By Ashley Liu.
At 677 W. 19th St. in Tempe, Arizona, you can see a one-of-a-kind home for yourself. At a glance, you’ll notice that the walls look a little unusual: they seem to be laid in horizontal layers. That’s because all of the home’s internal and external walls are 3D-printed.
Just as unique as the home’s construction method is the team that brought it to life. This project was nonprofit-driven: Habitat for Humanity Central Arizona spearheaded the project in partnership with the City of Tempe. The project also relied on pro bono contributions from various organizations, including Germany-based printer manufacturer PERI and Scottsdale-based architecture firm Candelaria Design. Candelaria provided the home with extra design flair, including exterior columns, transom windows, and even a 3D-printed kitchen island.
As Habitat for Humanity’s first 3D-printed home in Arizona, 677 W. 19th St. is quite literally a landmark accomplishment. But the home is also emblematic of a broader trend in construction across the world.
The Rise of 3D-Printed Construction
Over the past several years, 3D-printed homes have begun sprouting up across the country, from Texas to Virginia. While these projects are generally one-off custom homes, Arizona is one of the few states that has begun pioneering full-fledged housing developments. In Casa Grande, Arizona, a community of forty-two 3D-printed homes became available for sale in late 2022. This development was a solid demonstration of the efficiency of 3D-printing construction methods: from start to finish, each home purportedly took less than six weeks to build.
Internationally, 3D-printed construction has taken on even bolder and more imaginative forms. In Jiangsu, China, a 5-story apartment block was modularly printed and assembled in 2015. Dubai debuted the world’s largest 3D-printed building in early 2020. In Malawi, Africa and Nacajuca, Mexico, affordable 3D-printed housing and school building projects are underway.
3D-printing also represents a pathway for using new and improved materials in construction. While existing structures have largely been printed with concrete-based mixtures, they may soon be printed with plastics, metals, and even living organisms such as mushrooms.
To keep pace with innovation in the rest of the world, U.S. builders would benefit from staying abreast of the unique legal challenges posed by this novel construction method.
Legal Challenges: Securing the Building Permit
When Habitat for Humanity began its Tempe project, there was no existing building code provision for 3D-printed homes. Habitat relied on Section 104.11 in the International Building Code, which allows for “alternative materials, design, and methods of construction” that demonstrably meet or exceed code-prescribed methods.
To make this required demonstration, Habitat compiled study reports, testing reports, and data sheets, relying on third-party engineers rather than city inspectors. Due to the unconventionality of the building method, Habitat ultimately leaned on the City of Tempe’s highest levels of leadership for support. For ten of the nineteen months taken to plan the project, city officials participated in Habitat’s weekly calls.
The 2021 International Residential Code has since adopted Appendix AW to incorporate 3D-printed construction techniques. It remains, however, for state and local jurisdictions to modify their building codes to accommodate 3D-printing.
Legal Challenges: Who Bears the Risk?
In the realm of construction projects, Habitat’s Tempe home was highly novel in yet another respect: there was basically no written contract. This was largely due to the pro bono nature of the project; PERI donated the 3D printer, and Habitat’s volunteers supplied the labor. The only substantive contracts at play were a nondisclosure agreement—which protected the proprietary recipe for the printer’s concrete slurry—and a mortgage agreement for the family who ultimately moved into the Habitat home.
Perhaps the lack of contractual formality was crucial in this novel project setting, which turned out to be a learning process for everyone involved. To begin with, the German printer required conversion to American electrical specifications and units of measurement. When it came time to start building, the printer suffered from WiFi interruptions, computer crashes, and printer software malfunctions. Arizona’s 115-degree summers also posed certain problems. While the printer could run for up to six hours at a time in Germany, the Habitat team quickly discovered that Arizona’s extreme temperatures severely impacted print quality. As a workaround, the team ran the printer only for around two hours per day, concluding each day by eleven o’clock AM.
Despite being experimental and forgiving, the Habitat project still needed to manage certain risks. One key challenge was identifying an engineer of record who would be willing to accept liabilities and stamp plans for structural integrity. Another necessary adjustment was extending the warranty period: because the printed concrete’s durability was yet unknown, Habitat extended its warranty from two years to five years. In addition, Habitat needed to assemble a team of contractors who were neither accustomed to nor familiar with the printing technology. To smooth this over, Habitat involved tradespeople in its planning calls from the outset of the project.
Through its nonprofit-driven partnership, Habitat’s Tempe project sidestepped many of the risk-shifting challenges typically seen in construction law. The project nevertheless highlights some of the key risk management considerations that builders will continue facing in the realm of 3D-printed construction. Going forward, builders should continue to plan for the inherent risks of defective workmanship and delay that come with placing a 3D printer in a novel environment. 3D-printed construction can also expose additional parties to liability, including third-party engineers, 3D printer manufacturers, and even software engineers.
Conclusion
While 3D-printed construction has yet to reach widespread adoption in the U.S. and worldwide, it represents a promising solution in terms of both scalability and affordability. To develop a 3D-printed home in Tempe, Habitat for Humanity formed a unique collaboration with non-profit, public, and for-profit partners. While this team structure enabled the project to dodge certain legal obstacles, the project still illustrates valuable risk management lessons for future 3D-printed construction projects.
To keep pace with innovation in the rest of the world, U.S. builders would do well to pay attention to the evolving legal framework of 3D-printed construction. Most importantly, U.S. builders can continue looking out for the adoption of 3D-printing provisions in their local building codes.
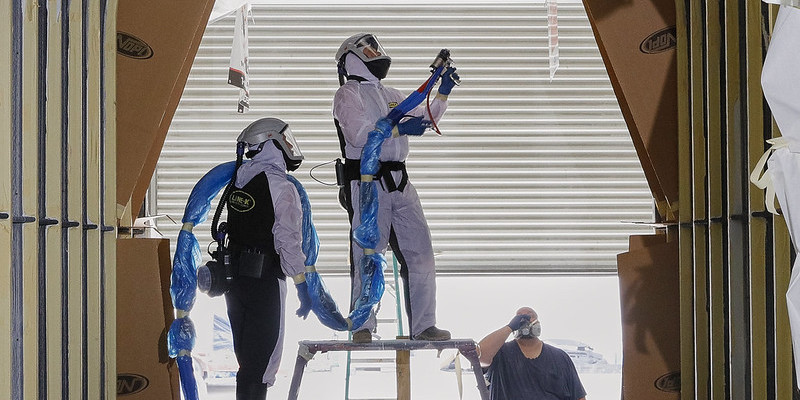
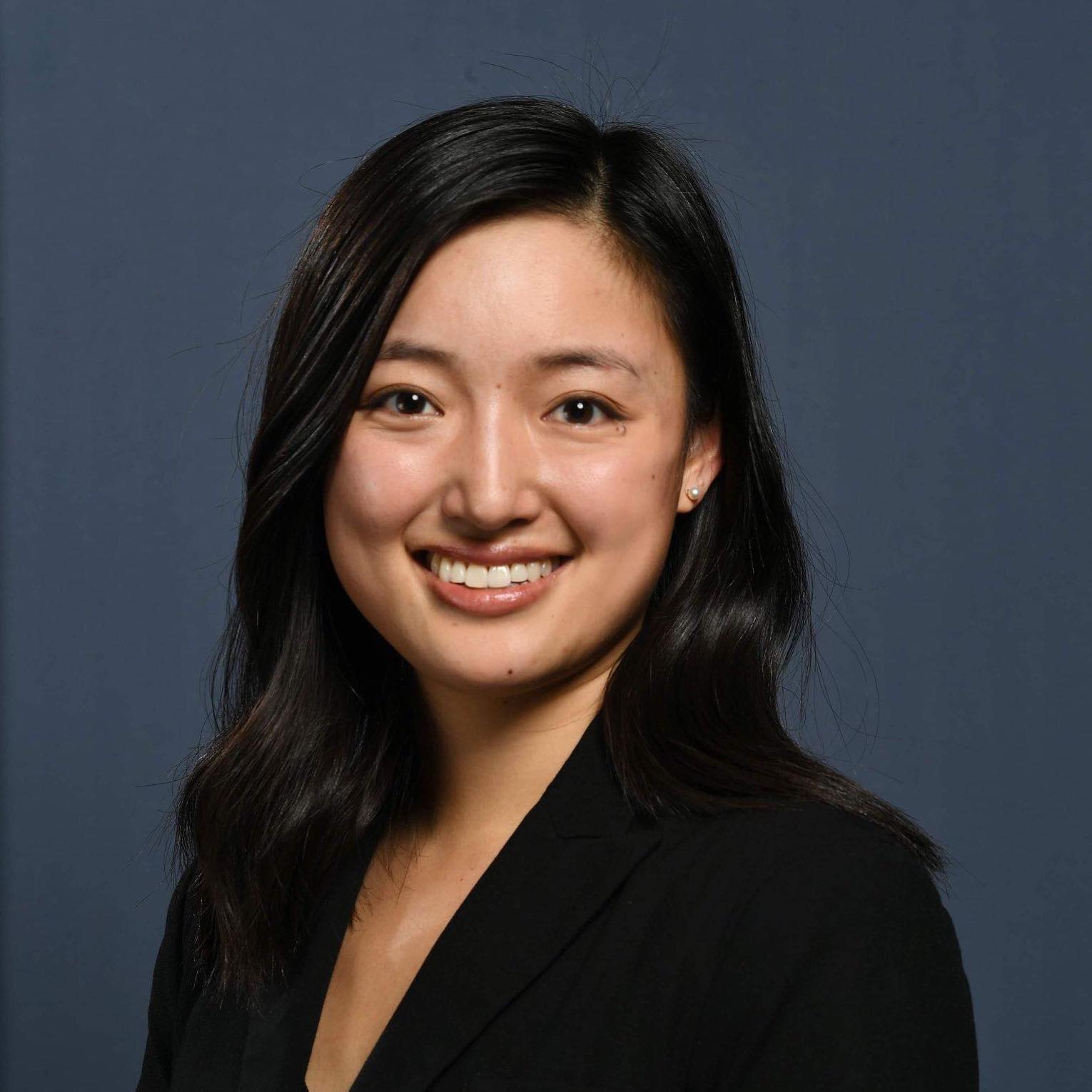
Ashley is a 2L from the San Francisco Bay Area. Before attending law school, Ashley worked as a statistical programmer and policy analyst at a healthcare policy think tank. Outside of school, Ashley enjoys hiking and spending quality time with her husband and rambunctious puppy.